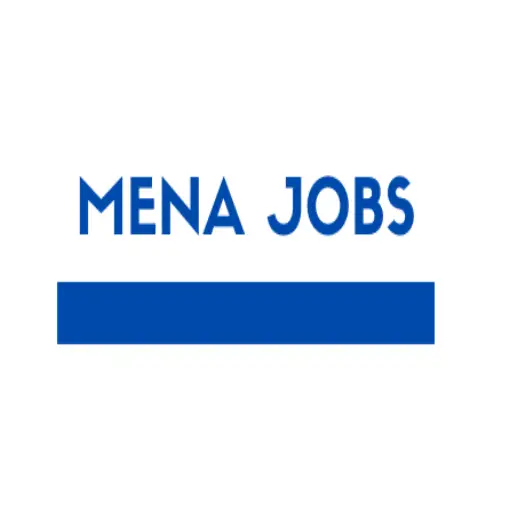
The Coca-Cola Company
To collect and summarize plant operation data/indicators for strategic analysis and improvement of plant operation in line with achieving the business objectives and goals
To be delegated for PLCR Manager’s role when required.
To perform as a power user of PP Module and IBP in SAP
C) Key Result Areas
Master Production Scheduling
- Establish the master production schedule to achieve the company objectives related to customer service, resource/capacity utilization and optimal inventory level.
- Execute rough-cut capacity planning to analyze the master production schedule.
- Managing and tracking the accuracy and effectiveness of the master schedules to continuously improve the overall master scheduling process.
- Lead monthly/weekly MPS meeting with Production, QSE and Supply Chain Service team and optimize monthly production schedule to respond timely to the situational changes and reflect them to the schedule.
- Liaise with Material Schedulers, QSE, Production areas and Customer Services as appropriate
- Support weekly schedule to ensure short-term manufacturing needs are agreed and monitored on a weekly basis on formal MPS meeting. Capacity plan is taken into consideration.
Capacity Planning
- Review the production capacity to reflect it to the production schedule on a daily, weekly, monthly basis by monitoring the daily production capacity.
- Lead weekly MPS meeting to discuss and set up the production schedule update and other operational status
- Evaluate capacity to ensure that potential bottlenecks are identified and necessary action is taken.
- Prepare capacity planning process to make sure that demonstrated capacity and review critical work center on a regular basis
- Capacity & productivity factors are reviewed regularly. Process exists and system is updated to reflect current.
Analysis and Support for process optimization
- Coordinate daily, weekly and monthly cycle count and set up yearly full count plan and report.
- Analyze plant operations data such as sales, production, inventory and other KBI’s monthly to report to management and communicate with plant associates for improvement of plant operations
- Review SAP Planning Parameters for efficiency in scheduling.
- Support to operators for trouble shooting in SAP.
- Improve operating efficiency, plant utilization and packaging rationalization by reducing areas of material wastage and/or line inefficiency.
- Participate in development of productivity enhancements for the operations.
- Lead Material Review Board (MRB) routine with plant stakeholder and Business stakeholders.
- Support to get feedback and coordinate sampling process for new product development.
Core Competency
D) Job Requirements / Qualifications
Drive Innovative Business Improvements
Balances Immediate and Long-Term Priorities
Delivers Results
Imports and Exports Goods ideas
Develops and Inspires Others
Lives the Values
- Concentrate Production (Competent)
- Beverage Production (Awareness)
- Packaging Materials Production & Supply (Awareness)
- Concentrate Equipment (Awareness)
- Ingredients Production & Supply (Awareness)
- Supply Chain Management (Proficient)
- Demand Management & Capability Planning (Proficient)
- Cost-of-Goods Management (Awareness)
- Import & Export Management (Awareness)
- Project Management (Competent)
- Safety, Health & Security Management (Awareness)
- Risk Analysis/Management (Awareness)
- Technical Standards, Specifications & Policies (Awareness)
- Statistic Process Control (Awareness)
- Product Development Process (Competent)
- Government Regulations – Manufacturing Plant (Awareness)
- Government Regulations – Food Laws (Limit)
- Food Science and Technology (Limit)
Knowledge & Experience
- 3~5years experience in a planning role – with operations/SAP PP, MM module and IBP experience preferred
- Lean & 6 Sigma experience preferred
Education & Professional Qualification
- BA degree. Preferably in technical or engineering.
- Thorough understanding of MPS & MRP
- Strengths in analysis and planning
- Basic finance knowledge
- Leadership and strategic thinking. High integrity and commitment.
- Problem Solving
- Innovative approach to translate plans into action.
- Strong interpersonal and management skills.
- Excellent communication and presentation skills
- Highly computer literate, particularly in Excel
Skills
Logistics; Warehouse Logistics; Business Processes; Data Anlaysis; Customer Service; Supply Planning; Project Management; Budget Management; Supply Chain Operations; Microsoft Office; Communication; Logistics Planning; Shipping; Problem Solving; Inventory Management; Order Fulfillment
Our Purpose And Growth Culture
We are taking deliberate action to nurture an inclusive culture that is grounded in our company purpose, to refresh the world and make a difference. We act with a growth mindset, take an expansive approach to what’s possible and believe in continuous learning to improve our business and ourselves. We focus on four key behaviors – curious, empowered, inclusive and agile – and value how we work as much as what we achieve. We believe that our culture is one of the reasons our company continues to thrive after 130+ years. Visit Our Purpose and Vision to learn more about these behaviors and how you can bring them to life in your next role at Coca-Cola.
We are an Equal Opportunity Employer and do not discriminate against any employee or applicant for employment because of race, color, sex, age, national origin, religion, sexual orientation, gender identity and/or expression, status as a veteran, and basis of disability or any other federal, state or local protected class. When we collect your personal information as part of a job application or offer of employment, we do so in accordance with industry standards and best practices and in compliance with applicable privacy laws.
/flavormanufacturing
R-68881
To apply for this job please visit careers.coca-colacompany.com.