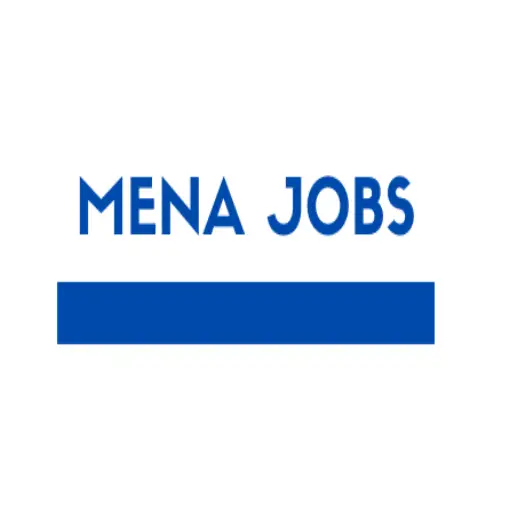
Moen Incorporated
The Supply Chain Analyst is a member of the Global Inventory Management Team which includes support of both Moen and the House of Rohl and will be engaged in a number of cross functional activities ranging from supporting business cycle activities like S&OP, to supply chain & related master data policy development to strategic projects to supply chain network modeling and optimization.
This role works to support the team goals of the Global Inventory Management Team which are inventory and working capital performance as well as the overall business objectives. Aside from reporting and analysis the Supply Chain Analyst may lead discussions with various functional areas in the supply chain and the business units, often cross functional.
RESPONSIBILITIES:
- Analyze, maintain, participate and own systems for setting safety stock and supply chain master data settings. This includes maintaining the process, validating data, identifying data issues, and working directly with functional parts of Fortune Brands Global Plumbing Group that have related process requirements. Establish standard methodologies for evaluating requests for safety stock changes by others. Track and maintain various safety stock fields such as coverage profiles, manual safety stock, and safety time.
- Perform inventory “What-If” modeling in Inventory Optimization software to determine inventory impacts related to changes in the supply chain.
- Analyze and provide linkage between demand signals and work center capacities by conducting aggregate evaluations of the work output of the master schedulers, the forecast changes passed from demand management, and the load changes at individual work centers. Identify data issues, timing issues, and provide expert analysis. Establish standard processes and ensure consistency in supporting decision making.
- Implement new complex supply chain initiatives related to inventory and capacity as needed. This may include creating project plans, facilitating functional buy-in across Moen, providing detailed data validation and testing, creating functional training documentation, training, and offering user support to functional groups as responsibilities are handed off in the organization.
- Analyze service performance, inventory levels and premium costs required to deliver Quantity-On-Time improvements to target stock levels. Make recommendations to improve inventory performance and work with the appropriate functional managers and teams to ensure metrics are achieved.
Plan / Deliver
- Support monthly Rough Cut Capacity Process (RCCP) and Sales and Operations Planning (S&OP) process by creating capacity analysis reports. Support global inventory health management across various value streams in the U.S., China, Canada, and Mexico.
- Monitor and maintain accurate data in SAP while also providing insight and recommendations for supply chain master data policy updates.
- Support continued integration of other business units into corporate supply chain processes
- Perform other responsibilities, which may include but are not limited to, material master governance over key fields that impact supply chain processes, inventory forecasting to support S&OP process, as well as supporting new products, productivity projects, and other product changes to smoothly transition to the new product and minimize obsolete material. Work with project teams as necessary to execute the planned transition on time.
System Design
- Utilize Right Sized Inventory and SAP to optimize inventory targets.
- Assist in automating reports from QlikView, QlikSense, VBA, JMP and SAP to support robust processes, troubleshoot problems and develop solutions.
- Continuously model excess inventory to determine and eliminate root causes
- Provide analytical support for life cycle modeling including new product introduction and End of Life
- Utilize various tools to gather and analyze trends for the purpose of adjusting supply plan activities.
- Assist with training cross-functional teams in multiple plants, including Asia, in process enhancements. Create robust and detailed training materials.
Qualifications
- Bachelor’s Degree is required. A degree in Engineering, Supply Chain Operations or a related field is preferred.
- Minimum of 3 years of experience in supply chain management, including experience in multi-echelon inventory optimization, with at least two years in a manufacturing environment. A Master’s Degree may offset up to two years of experience.
- SAP experience is preferred.
- CPIM, CSCP, CPF, or Lean certifications are a plus.
- Proficient use of R, Python, Java, SQL, SAP or other flexible programming languages is preferred.
- Ability to communicate effectively and influence outcomes. Strong verbal and written communication skills and the ability to establish cross functional relationships.
- Understanding of engineering, manufacturing, sourcing, finance, supply chain principles and demand/supply planning.
- Skill in data consolidation, analysis and presentation tools such as Microsoft Access, Microsoft Excel, SAS JMP as well as detailed knowledge of MRP and pull systems. Knowledge of single and multi-echelon inventory optimization software; Logility Voyager and Right Sized Inventory preferred.
- Demonstrated strong analytical capability as well as experience in process design/redesign and problem solving is required.
- Familiar with basic GAAP concepts as inventory, accounts payable, accounts receivable and working capital pertains to the balance sheet, income statement and cash flow statement.
To apply for this job please visit www.linkedin.com.